En el corazón de la Selva Negra, lejos de la niebla salina, Holger Bührle construye Hulg, una goleta de aluminio de 22 metros. Durante 25 años, este autodidacta ha dedicado su vida a un proyecto extraordinario, una obra que combina destreza técnica e ingenio. En esta primera parte, repasamos un proyecto único, en el que cada etapa encarna la perseverancia y el sueño de dar la vuelta al mundo.
El nacimiento del sueño de toda una vida
Holger Bührle no es un constructor naval tradicional. Electricista de formación, se dedicó a la navegación por pasión, aunque vive a más de 500 km del océano. Esta distancia geográfica nunca le ha frenado, sino todo lo contrario. '' Si hubiera tenido que esperar a estar junto al mar para empezar, nunca habría hecho nada.. confiesa.
Su pasión por el mar se remonta a su adolescencia, mucho antes de su proyecto de construcción. Nacido en la región de Baden, descubrió la vela a los 14 años en el lago Schluchsee, donde obtuvo la licencia A. Fue amor a primera vista. Fue amor a primera vista. Después navegó muchas veces por el mar, sobre todo con su tío en el sur de Francia y en Grecia, lo que reforzó su deseo de vivir de esta pasión. Empezó con lanchas neumáticas, luego se aventuró en un Tornado, pero la llamada del mar abierto era apremiante.
En 1998, realizó su primera travesía del Atlántico a bordo del Kritter, un dos mástiles de 25 metros. Esta travesía marcó un punto de inflexión en su carrera y le inspiró para diseñar un barco capaz de dar la vuelta al mundo a vela, que fuera duradero y apto para una tripulación reducida. Fue al descubrir los planos de hydraduo diseñado por el arquitecto naval Kurt Reinke, que Holger Bührle sentó las bases de su proyecto. Inspirándose en estas líneas, decidió adaptar el diseño a sus propias ambiciones.
El proyecto comenzó modestamente en su jardín, lejos del mar, en medio de las colinas boscosas de la Selva Negra. Esta distancia geográfica, lejos de ser un obstáculo, se convirtió en el símbolo de un reto personal para Holger. '' Construir un barco aquí significa convertir un sueño lejano en una realidad tangible, día tras día dice.
Errores en la formación
Autodidacta, aprende las técnicas de construcción naval a través de la investigación, la experimentación y los errores, que considera parte esencial del proceso. En cada etapa de la construcción, se impone a sí mismo las normas de calidad que considera necesarias para las condiciones extremas a las que quiere enfrentarse en el mar. La elección del aluminio, un material robusto y ligero, se hizo rápidamente por su resistencia a la corrosión, esencial para las largas travesías en un entorno aislado. '' No es sólo un barco lo que estoy construyendo, es una visión de la libertad y la autosuficiencia explica. Este sueño se traduce en una búsqueda de la perfección que le impulsa a trabajar día tras día, a veces solo, a veces con la ayuda de entusiastas que vienen a echarle una mano.
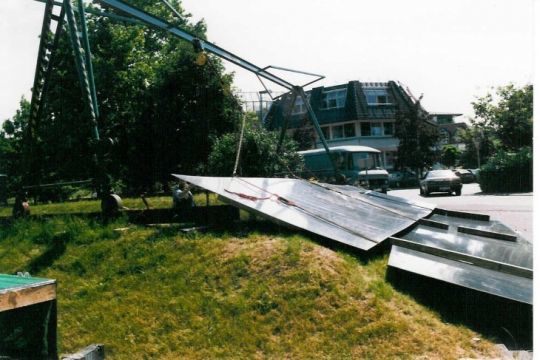
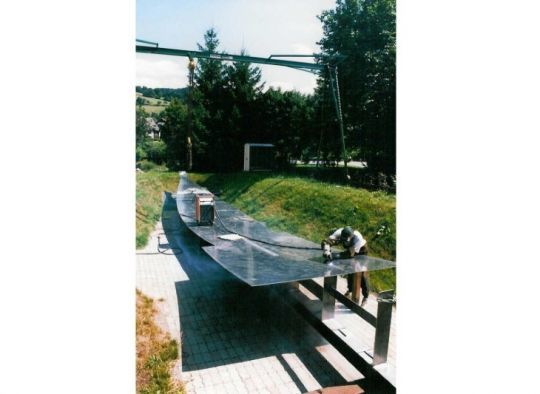
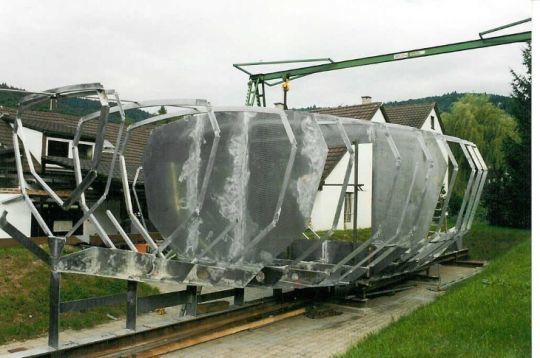
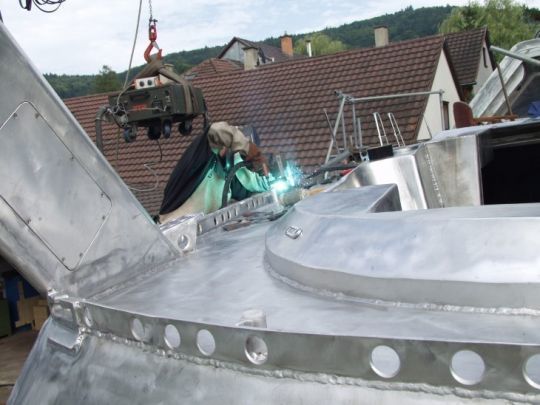
El casco: procesos exigentes
El casco de aluminio es el corazón técnico del Hulg. Con su diseño de quilla larga, confiere al barco una buena estabilidad al tiempo que limita su calado a 2 metros. Esta arquitectura garantiza un buen comportamiento a vela y facilita la varada en caso necesario.
El uso de paneles de aluminio marino de alta calidad, cortados y soldados a mano con precisión quirúrgica, ha reducido el peso total de la embarcación al tiempo que garantiza una perfecta estanqueidad y una resistencia estructural óptima.
Los compartimentos estancos integrados en el casco, utilizados como depósitos de agua y combustible, no sólo aumentan la capacidad de almacenamiento, sino que también ayudan a equilibrar la embarcación cuando está en marcha.
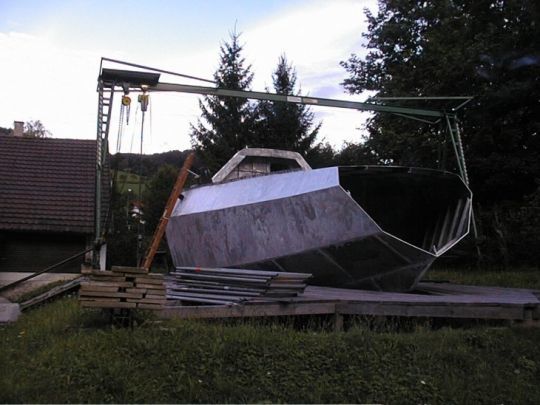
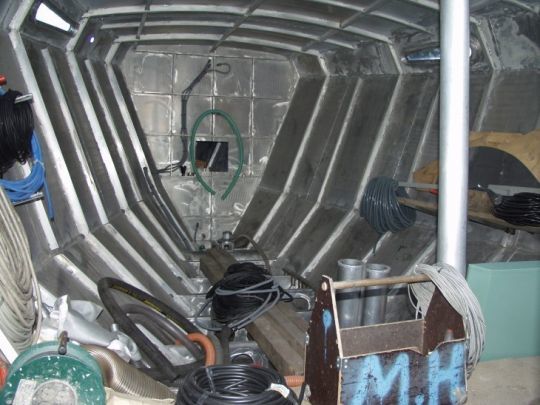
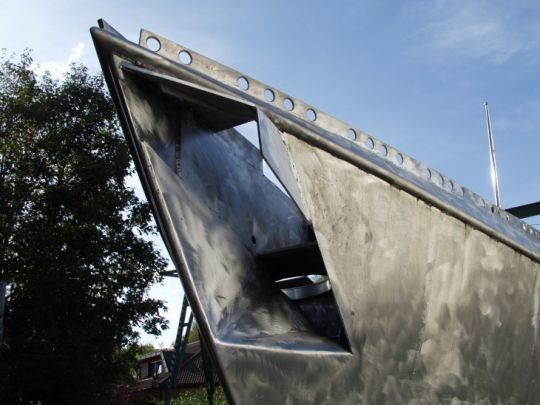
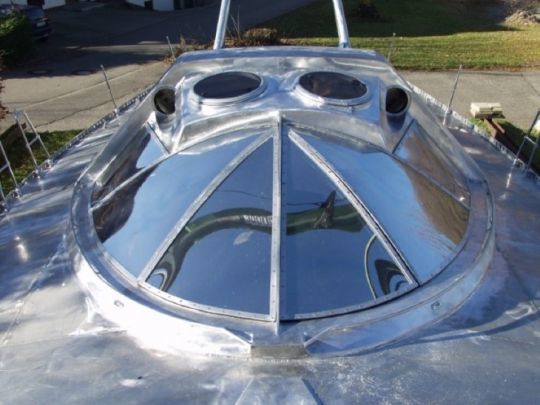
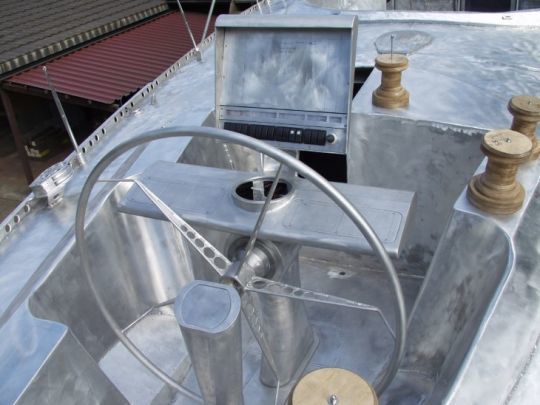
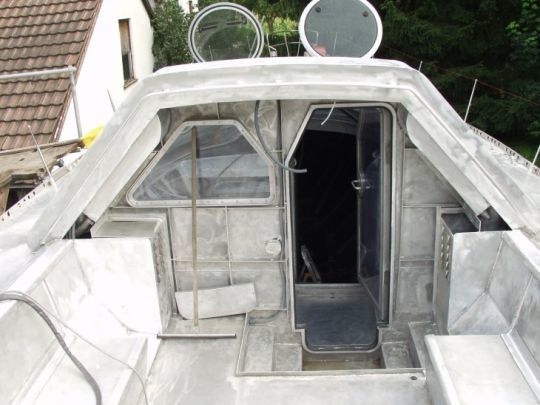
Fabricación de quillas: un proceso técnico
Holger optó por un enfoque meticuloso y pragmático para fabricar la quilla de su barco. El proceso comenzó soldando el molde. La quilla, que sólo estaba llena de plomo hasta la mitad, requería una placa intermedia para crear un depósito en la parte superior. Se añadieron orificios de soldadura auxiliares para permitir la extracción del combustible y la soldadura interna. El cierre de las placas de 8 mm en la proa fue todo un reto para Holger, ya que requirió una cuidadosa gestión del calor para evitar la distorsión de la quilla. El borde superior se dejó con un voladizo de 10 cm para futuros ajustes. Una vez colocado el molde, Holger tuvo que preparar el espacio bajo el barco para instalar la quilla. Se excavó el suelo y se utilizaron dos vigas de acero como raíles para deslizar la quilla bajo el barco. Debido a la adición de plomo junto al casco, hubo que encontrar una solución para desplazar la quilla 3 metros lateralmente utilizando una técnica inspirada en los métodos egipcios con rodillos abiertos.
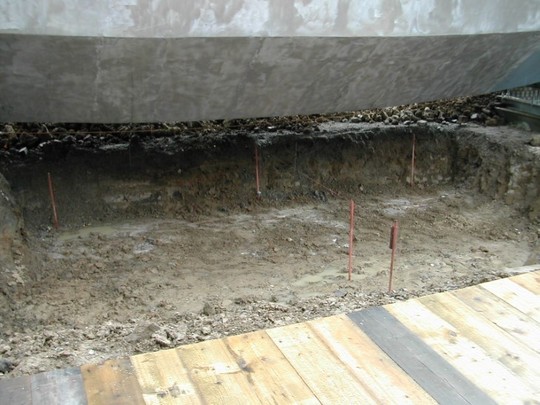
El vertido de plomo duró dos días sin parar. El trabajo era exigente, desprendía un humo amarillo que envolvía la zona residencial, mientras el equipo de Holger vertía el plomo en porciones de 100 kg, capa a capa. Cada capa de plomo tenía que enfriarse bajo el agua, lo que hacía la operación especialmente delicada. Tras un periodo de enfriamiento y regeneración, la quilla se ajustó a la plantilla. El ajuste final sólo tuvo lugar en la posición definitiva, donde el fuselaje descansaba sobre dos vigas de acero que podían ajustarse en altura mediante varillas roscadas. De este modo se compensaban los movimientos del suelo. Por último, una vez colocada la quilla, se biseló el borde y se aplicaron cuatro capas de soldadura para finalizar la fabricación de este elemento crucial de la embarcación.
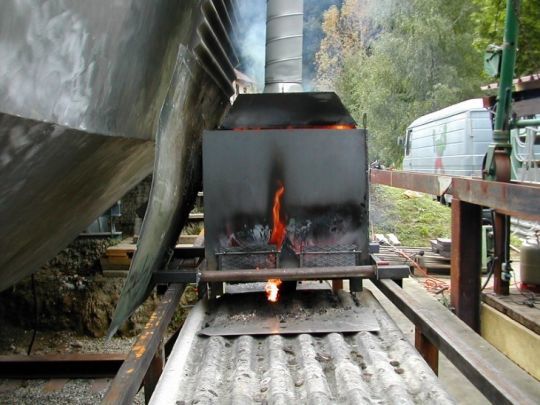
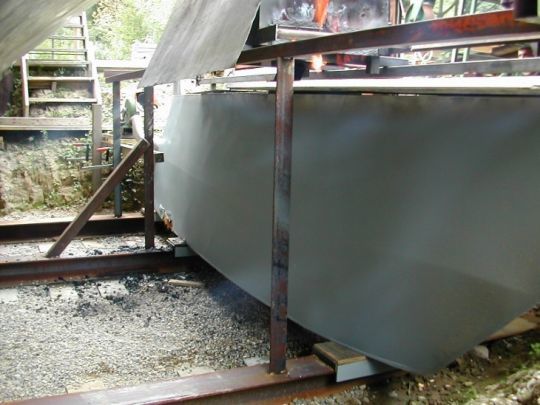
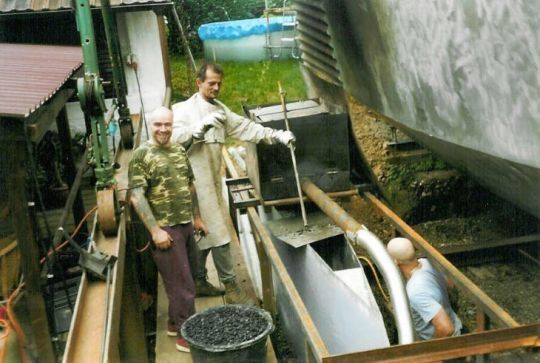
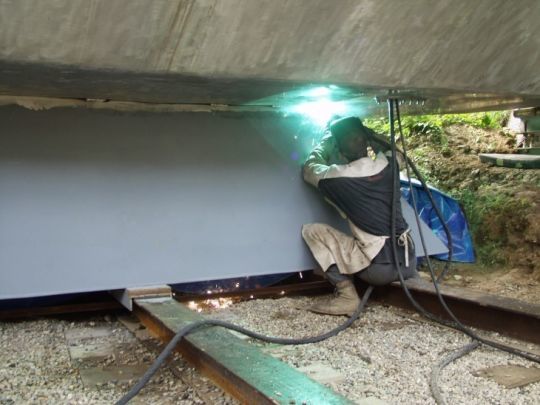
Un puente que resiste el paso del tiempo
La cubierta, revestida de teca de 8 mm, descansa sobre una placa de apoyo de 6 mm diseñada para limitar los efectos de las variaciones de dilatación. Para todas las operaciones de rejuntado y pegado, Holger eligió productos Sika, en particular el compuesto de nivelación, especialmente eficaz para corregir las irregularidades que se observan con frecuencia en una cubierta metálica. Su objetivo era mantener la cubierta lo más despejada y fluida posible, un enfoque ilustrado por la integración de grandes cornamusas de amarre desplegables XXL, que son discretas cuando están plegadas.
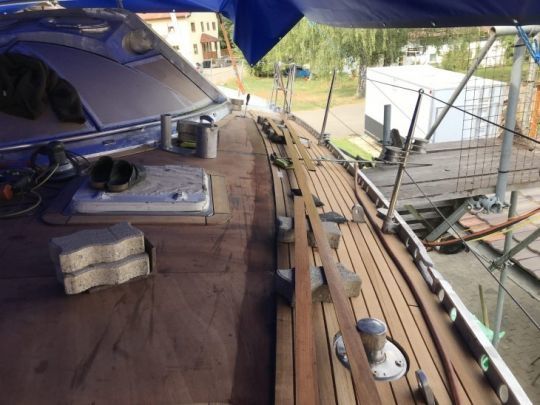
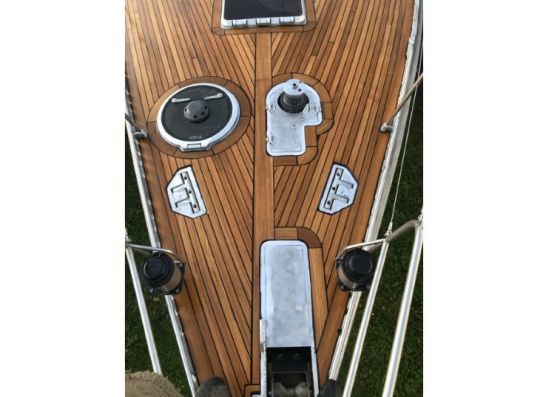
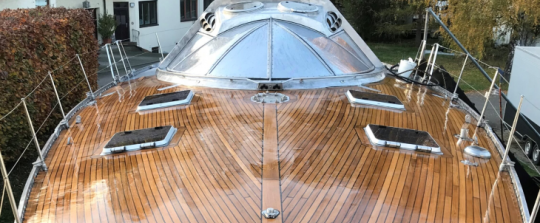
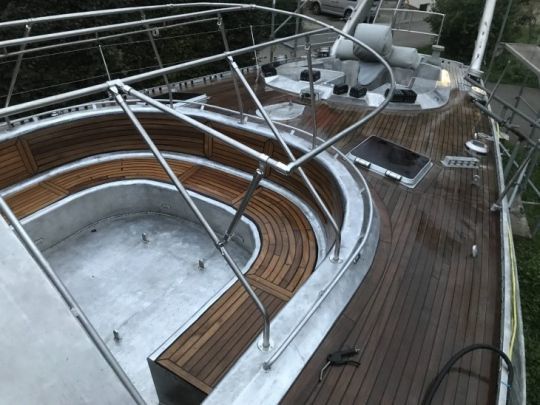
Un aparejo diseñado para ofrecer rendimiento y durabilidad
Con un mástil principal de 22,5 metros y un mástil de mesana de 19,5 metros, el yate se beneficiará de una gran superficie vélica. Las modernas velas de sables completos se montarán en sistemas de carros de rodillos para facilitar su manejo. Los winches, enrolladores de foque y sistemas tensores se accionarán hidráulicamente, una proeza técnica que proporciona comodidad y precisión en todas las condiciones.
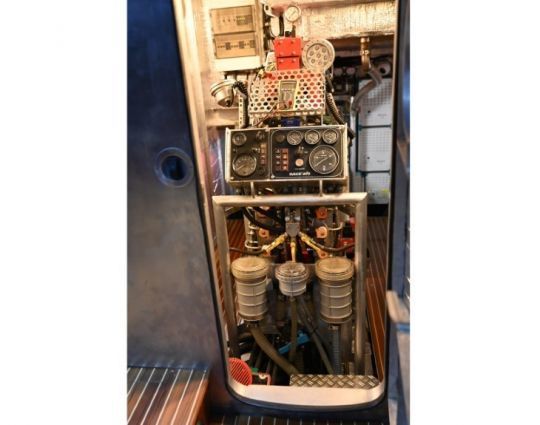